I recently built 4 TriTrix TL's and love them, but, it got me very interested in quarter wave transmission lines. I have an idea rattling around in my head and the very attractively priced Dayton SD270-88 put my idea into action. But, before I make chips fly I thought I would throw my idea out there for some criticism or other input.
My idea is to make something that looks like this:
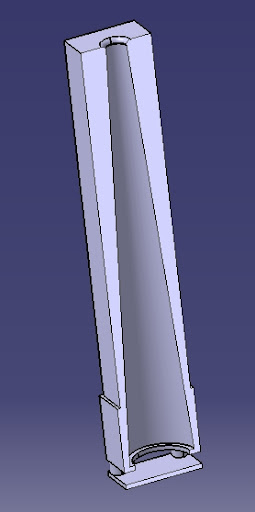
I'm going to call it the MASONIC 10:69. I'm going to call it this because it will be made out of 564 layers of 1/8th inch thick Masonite, which will make a tapered quarter-wave transmission line 69 inches long. The 10 comes from the fact that I'm using a 10 inch woofer.
After a LOT of reading from the material on quarter-wave.com I think I finally figured out what I had to do to make this work. The first thing to do was to pick a driver. PE getting rid of their shielded SD270-88 subwoofers provided that opportunity. From the driver parameters you find the Fs, which is 30Hz in this case. The other parameter mentioned is Qts with a recommended value of .4 ish, this driver has a Qts of .44, so I thought it was close enough. The other benefit of using this driver was it has the same Fs of several of the other higher quality 10" drivers from PE, so if I don't like the driver I can just swap it out. After picking the driver I used the alignment tables from Mr. King, and using a 0.1 SL/S0 I found the length to be 68.9 inches (which I conveniently rounded to 69 inches). I have included this information on the second page of the attached file. The Bottom is 13"x13". I thought that having an 11" diameter hole just inside the baffle would be fine, but I'm not really sure if that is enough breathing room for the woofer (any suggestions?), and that calculated out to a 3.5" diameter opening on the top in order to follow the 0.1 SL/S0 recommendation.
After that I got busy on the math and came up with a hole diameter for every layer in my 564 layer stackup. The information for that is on page 1 of the attached file. The first 6 and last 6 layers are different than the rest because on the bottom the last 6 layers are for the mounting of the driver.
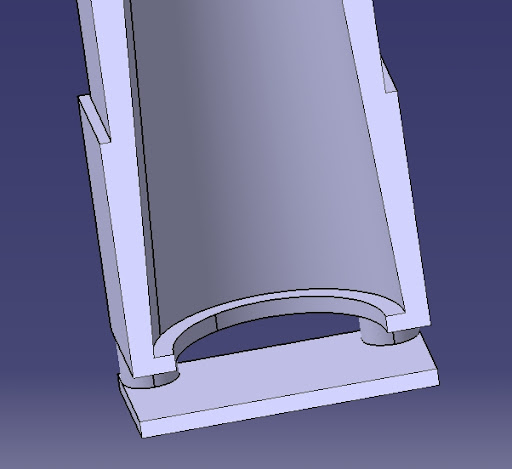
The top 6 layers are for the end port roundover.
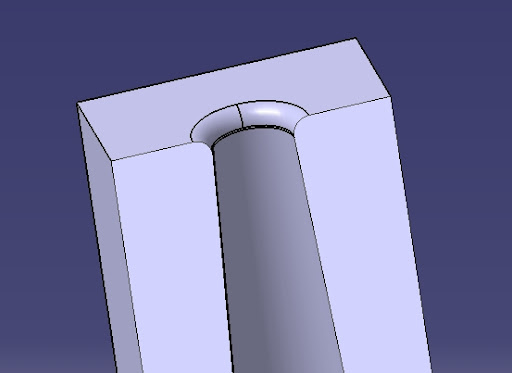
I want to use the information in the tables to cut the correct diameter hole in every level, then glue the levels together with either contact cement or some other glue concoction. I don't really want to use contact cement because of the wait after application before install (usually about 15 min), and the inability to move the layers once they touch, so...if you have any suggestions here please speak up.
In the end these will be about 74 inches tall (just over 6 feet). They have a step at 10 inches tall so that I can drop my layer sheet size down to a 12"x12" square instead of a 13"x13" square helping me get more squares out of a sheet of Masonite (32 instead of 21), fortunately for me I have a near limitless supply of VERY cheap Masonite available...I think it'll cost me about $0.80 for ALL the Masonite for this project (approximately 22 sheets).
I'm hoping that by doing a TQWT that tapers in a cone instead of just in 1 dimension that I will get better bass extension on the first system resonate frequency, which should be in the low 20Hz area. But, I have a lot of work ahead of me before that! Good thing I have a hole cutter on my Dremil Tool that works perfectly on Masonite...
It is going to take me a while before I get this completed (even though the speaker gets here today!), so if you have any input please feel free to make any criticisms or suggestions...especially if you think I'm exceptionally crazy in thinking this will work.
My idea is to make something that looks like this:
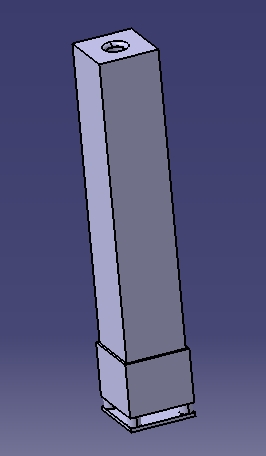
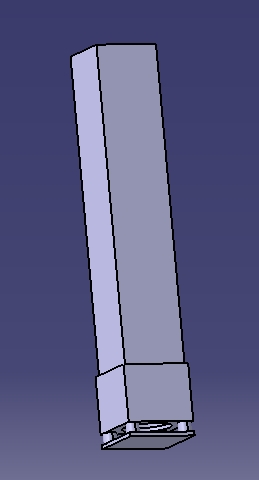
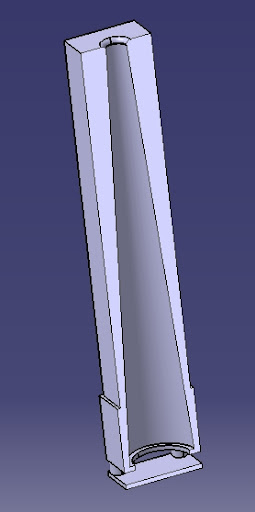
I'm going to call it the MASONIC 10:69. I'm going to call it this because it will be made out of 564 layers of 1/8th inch thick Masonite, which will make a tapered quarter-wave transmission line 69 inches long. The 10 comes from the fact that I'm using a 10 inch woofer.
After a LOT of reading from the material on quarter-wave.com I think I finally figured out what I had to do to make this work. The first thing to do was to pick a driver. PE getting rid of their shielded SD270-88 subwoofers provided that opportunity. From the driver parameters you find the Fs, which is 30Hz in this case. The other parameter mentioned is Qts with a recommended value of .4 ish, this driver has a Qts of .44, so I thought it was close enough. The other benefit of using this driver was it has the same Fs of several of the other higher quality 10" drivers from PE, so if I don't like the driver I can just swap it out. After picking the driver I used the alignment tables from Mr. King, and using a 0.1 SL/S0 I found the length to be 68.9 inches (which I conveniently rounded to 69 inches). I have included this information on the second page of the attached file. The Bottom is 13"x13". I thought that having an 11" diameter hole just inside the baffle would be fine, but I'm not really sure if that is enough breathing room for the woofer (any suggestions?), and that calculated out to a 3.5" diameter opening on the top in order to follow the 0.1 SL/S0 recommendation.
After that I got busy on the math and came up with a hole diameter for every layer in my 564 layer stackup. The information for that is on page 1 of the attached file. The first 6 and last 6 layers are different than the rest because on the bottom the last 6 layers are for the mounting of the driver.
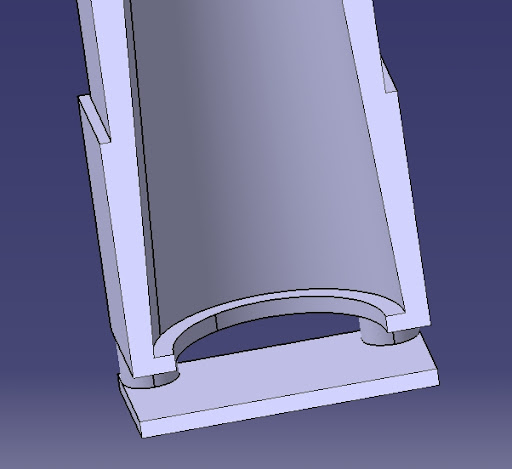
The top 6 layers are for the end port roundover.
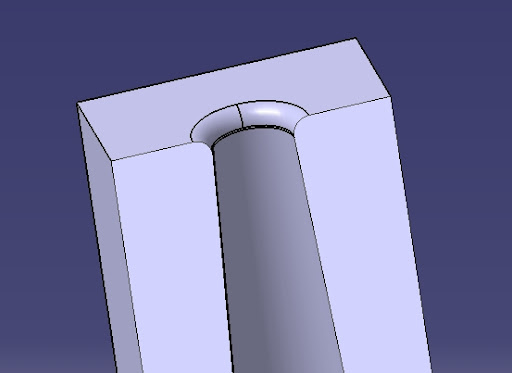
I want to use the information in the tables to cut the correct diameter hole in every level, then glue the levels together with either contact cement or some other glue concoction. I don't really want to use contact cement because of the wait after application before install (usually about 15 min), and the inability to move the layers once they touch, so...if you have any suggestions here please speak up.
In the end these will be about 74 inches tall (just over 6 feet). They have a step at 10 inches tall so that I can drop my layer sheet size down to a 12"x12" square instead of a 13"x13" square helping me get more squares out of a sheet of Masonite (32 instead of 21), fortunately for me I have a near limitless supply of VERY cheap Masonite available...I think it'll cost me about $0.80 for ALL the Masonite for this project (approximately 22 sheets).
I'm hoping that by doing a TQWT that tapers in a cone instead of just in 1 dimension that I will get better bass extension on the first system resonate frequency, which should be in the low 20Hz area. But, I have a lot of work ahead of me before that! Good thing I have a hole cutter on my Dremil Tool that works perfectly on Masonite...
It is going to take me a while before I get this completed (even though the speaker gets here today!), so if you have any input please feel free to make any criticisms or suggestions...especially if you think I'm exceptionally crazy in thinking this will work.
Comment